Enviropeel Saves $113k Annually on Bearings
- Omar Obaid
- Mar 19
- 2 min read
Introduction:
The 153,200 Problem Hidden in Plain Sight ∗∗Imagine a Fortune 500−scalecompany—2,500employees,1.5B in annual revenue, producing enough fiber-board daily to build 750 homes—brought to its knees by a component smaller than a coffee mug. Bearings, the unsung heroes of industrial machinery, were failing every two weeks in this manufacturing giant, costing $153,200 annually. Slurry abrasion and paint contamination turned routine operations into a financial hemorrhage, with engineers replacing bearings 8x faster than industry standards.
Then came Enviropeel by IZOTECK
The Culprit: When "Business as Usual" Becomes a $73,000/Year Mistake
In the relentless production environment:
1.5 million square feet of fiber-board daily = 2.5 Olympic swimming pools of abrasive slurry
Thousands of bearings bombarded by corrosive particles and paint overspray
14-day lifespans for critical components meant 24/7 maintenance teams
"Engineers were stuck in a loop," says an Enviropeel technical lead. "Every bearing change halted production, but not changing them risked catastrophic downtime."
The Enviropeel Trial: 0 Failures. 100% Performance. A Manufacturing Revolution.
When the company greenlit a full-scale Enviropeel trial, skeptics expected incremental gains. What they got redefined "ROI":
100% bearing survival during the trial period
Engineers discovered zero contamination under the protective coating
Immediate order for expanded Enviropeel equipment/training
"Removing the coating felt like unwrapping a time capsule," recalls a plant engineer. "Bearings looked factory-new despite months in the slurry warzone."
The Numbers That Redefine Industrial Maintenance
Short-Term Win: 50% fewer replacements = $73,000 annual savings (conservative estimate)
Projected Reality: 6-month bearing lifespan = $113,100 saved yearly (74% cost reduction)
Historical Context: From 8 replacements/year to 1-2 – a 500%+ lifespan increase mirroring Enviropeel’s global track record
Why This Isn’t Just About Bearings
The implications ripple beyond maintenance budgets:
Downtime Avoidance: Every bearing swap halts production. Fewer swaps = uninterrupted revenue.
Scalability: If a 2,500-employee titan saves six figures, what could your facility achieve?
Future-Proofing: Enviropeel’s polymer technology adapts to harshest conditions – chemical, thermal, or abrasive.
The Silent Game-Changer: How Enviropeel Works
While technical details stay guarded, the science is simple:
Multi-Layer Defense: Bonds to metal, creating an impenetrable barrier against slurry/paint
Self-Healing Properties: Minor scratches? The coating reforms.
Non-Toxic: Unlike traditional greases, it won’t contaminate products or processes
Conclusion: Your Turn to Transform "Cost Centers" Into Profit Protectors
This $1.5B manufacturer isn’t special—they were just first to act. As Enviropeel’s team notes: "The only thing more expensive than maintenance is delaying maintenance."
Your Next Move:
✅ Calculate your potential savings with our Industry-Specific ROI Calculator
✅ Book a Free Contamination Audit with Enviropeel engineers
✅ Join the 217+ plants that added 7 figures to their bottom line
Because in manufacturing, the smallest components often hide the biggest opportunities.
Call to Action:
"Ready to extend your bearing service life by 500%"?
Contact IZOTECK Now – First 10 Respondents Get a Free professional consultation."
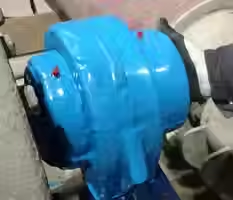
コメント