Faster Return to Service: EonCoat vs. Traditional Three-Coat Systems
- Omar Obaid
- Feb 18
- 2 min read
In 2017, a comparative study was conducted in Pascagoula, Mississippi, to evaluate the efficiency of EonCoat in preventing corrosion compared to a conventional three-layer paint system. Two storage tanks, each covering around 16,000 square feet, were selected for this test. One tank was coated with EonCoat, while the other underwent a traditional three-coat paint application.
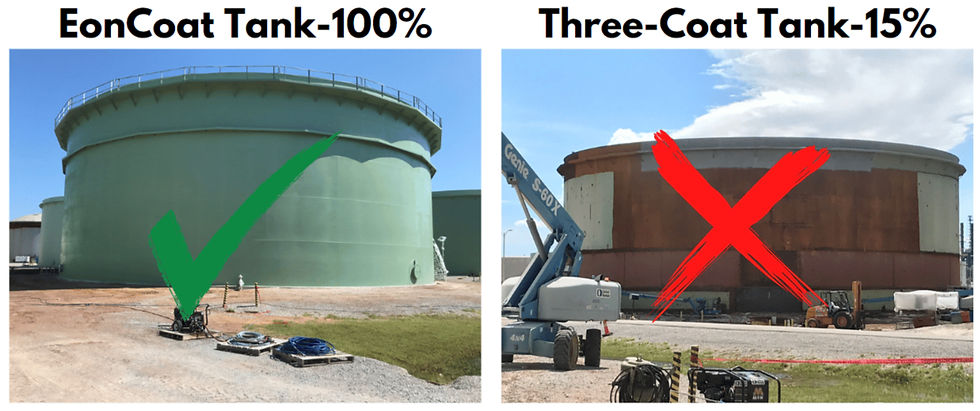
How Long Did the Applications Take?
Despite 22 rainy days in July 2017, the EonCoat-coated tank was fully completed in just nine workdays, excluding weather-related delays like lightning. Meanwhile, the traditional three-coat method progressed at a much slower rate—after the same period, only 15% of the surface was finished.
According to projections, the full application of the three-coat system would take about 54 days to complete. When EonCoat’s Lead Scientist, Sameer Patel, revisited the site in November, the traditional coating was still being applied.

Why Is EonCoat Faster?
Several factors contributed to EonCoat’s efficiency:
Simplified Surface Preparation: The entire tank was prepared at once, eliminating the need for staged blasting and coating. The preparation met SSPC-SP6 / NACE 3 / SA2 standards.
Unique Chemical Bonding: EonCoat, a chemically bonded phosphate ceramic (CBPC), forms an iron phosphate layer that alloys with the carbon steel, providing base-level protection. A second ceramic layer on top further reinforces corrosion resistance.
Single-Coat Application: EonCoat is applied using a high-pressure plural pump in a single step. The wet film thickness (WFT) is 30 mils, with a dry film thickness (DFT) between 24 and 28 mils.
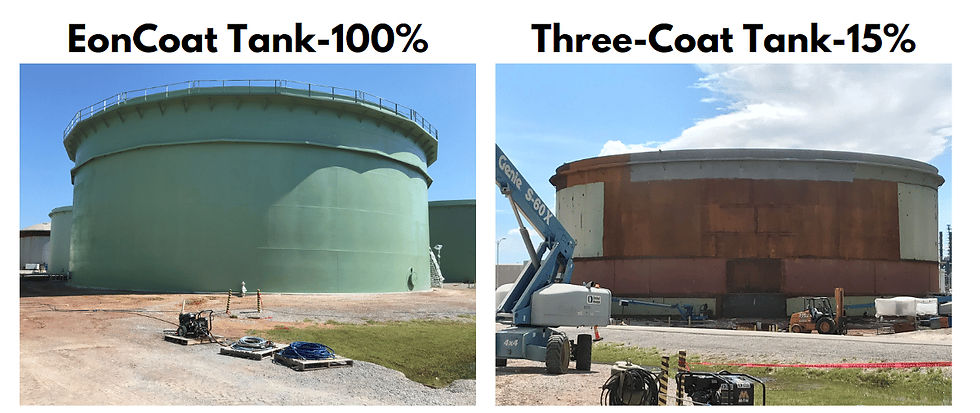
Challenges of the Three-Coat System
The traditional three-coat method involved a segmented approach, meaning small sections had to be prepared, primed, and coated individually. The process included:
Inorganic Zinc Primer – The first layer was applied after blasting.
Epoxy Midcoat – Required after the primer cured.
Polyurethane Topcoat – Final protective layer.
Each coat required specific curing times, causing delays. Weather conditions, including high humidity and rain, frequently led to flash rust, requiring re-blasting before continuing the application. This made the process significantly more time-consuming and labor-intensive.

Conclusion: A More Efficient Solution
This study demonstrated that EonCoat provides a significantly faster and more efficient corrosion protection alternative compared to traditional three-layer coatings. The ability to reduce labor hours, speed up curing time, and simplify surface preparation makes EonCoat a game-changer in industrial corrosion protection.
IZOTECK
Comments